Il nuovo polo logistico automatizzato di mantova, di 130.000 mq, interamente dedicato a Adidas e gestito da Kuehne+Nagel, è destinato allo stoccaggio della merce proveniente dal mercato internazionale e il suo indirizzamento verso il mercato del Sud Europa. L’intero centro, a emissioni zero di CO2, è alimentato al 100% da energie rinnovabili. La struttura, altamente tecnologica e al tempo stesso cantiere sostenibile, ha infatti conseguito la certificazione Leed Gold.
Il cantiere, gestito da Engineering2k, è iniziato a febbraio del 2022 ed è stato portato a termine in soli 2 anni di lavori. Il nuovo centro logistico si trova ad Olmolungo (Mn), in una zona pianeggiante incastonata tra l’uscita dell’autostrada A22, Modena – Brennero, il polo Enichem e l’inizio dell’idrovia Fissero-Tartaro-Canalbianco, dove è ubicato il porto di Valdaro.
L’area ha subìto negli ultimi decenni una rapida e massiva trasformazione ancora in corso, in seguito all’insediamento di fabbriche e imprese operanti nei settori dei trasporti e della logistica.
Inoltre, nel breve periodo, la zona potrebbe essere interessata dalla costruzione di un polo logistico intermodale e dal completamento del raccordo stradale che si inserirà direttamente sull’autostrada del Brennero.
La struttura è stata suddivisa in compartimenti e circondata da aree di pertinenza funzionali all’attività di deposito (parcheggi, strade e aree di manovra, piazzali di carico e scarico, aree verdi e bacini di laminazione per lo smaltimento delle acque piovane, locali tecnici per l’approvvigionamento energetico).

Un solo corpo edilizio
L’intervento presenta un unico corpo edilizio, all’interno del quale è svolta sia l’attività di ufficio che quella di magazzinaggio e movimentazione della merce, suddiviso in due aree principali:
- un magazzino logistico composto da 8 comparti (con la previsione di aggiungerne uno in futuro) organizzati in aree funzionali destinate allo stoccaggio del materiale;
- un blocco uffici su due piani destinato alla gestione dell’attività svolta nei comparti.
Struttura portante
Il magazzino è stato realizzato con una struttura portante prodotta da Isocell, costituita da:
- elementi prefabbricati in calcestruzzo armato precompresso (c.a.p. composta da travi primarie a “I” e travi secondarie (arcarecci) a “T” con resistenza al fuoco Rei120 e un livello di compartimentazione El120;
- un sistema di travi e pilastri prefabbricati in acciaio per la realizzazione dei mezzanini interni al deposito.
Involucro
Lo zoccolo dell’edificio è stato realizzato con pannelli prefabbricati in c.a.p. mentre per le tamponature sovrastanti sono stati utilizzati dei pannelli sandwich in Pir con baraccatura metallica di supporto e finitura metallica colorata. Questi ultimi sono caratterizzati da un alto potere isolante, resistenza all’acqua e all’umidità, bassa conducibilità termica, leggerezza e un’ottima resistenza al fuoco.
I tamponamenti perimetrali proseguono fino a un’altezza di 1,10 metri rispetto l’estradosso più alto della copertura, non rendendo necessario l’utilizzo in copertura di dispositivi di protezione per la caduta dall’alto (linea vita).
La soluzione ad angolo ha previsto la realizzazione di una vetrata strutturale a montanti e traversi, caratterizzata da un elemento decorativo rivestito da pannelli compositi costituiti da due lamiere esterne di alluminio e un nucleo interno (simile all’Alucubond).
Il montaggio dei pannelli alla sottostruttura metallica appositamente sagomata è stato realizzato mediante dei sistemi di fissaggio a scomparsa che rendono la superficie complanare. Tali pannelli possono essere infatti tagliati, fresati, curvati, smussati e piegati a piacimento a seconda delle esigenze e montati facilmente in cantiere grazie al loro peso contenuto.
Copertura
L’altezza del fabbricato non è uniforme su tutta l’impronta a terra: sono presenti tre altezze dettate dai rispettivi sistemi di stoccaggio e gestione delle merci: altezza di 13,95 m per l’area 1, di 17,96 m per l’area 2 e 26,73 per l’area 3.
La copertura è stata realizzata con struttura Bacacier (travi principali ed arcarecci) con finitura superficiale con manto Tpo con colorazione chiara e pendenza (1,5%) tale da garantire un deflusso delle acque verso il fronte est e ovest dell’edificio. Il pacchetto di copertura è stato realizzato (dal basso verso l’alto) con:
- un supporto strutturale in lamiera grecata;
- uno strato di isolamento rigido realizzato con pannelli Pir in poliuretano espanso rigido (materiale leggero ma resistente alle sollecitazioni di tipo meccanico);
- una barriera al vapore;
- un manto di copertura impermeabilizzante sintetico in Tpo bianco.
La scelta di questa stratigrafia ha garantito il corretto isolamento dell’aria interna al deposito, con rispetto del valore massimo di trasmittanza termica imposto dalla normativa nazionale energetica per la zona climatica di riferimento.
In copertura sono stati inoltre realizzati dei lucernari fissi e apribili; mentre in corrispondenza dei pannelli perimetrali sono state posizionate porte, portoni e baie di carico secondo le esigenze funzionali e distributive dell’edificio.
La copertura dell’impianto è stata infine rivestita da pannelli fotovoltaici in grado di produrre l’energia elettrica necessaria per fornire all’hub circa l’80-90% dell’energia necessaria e per soddisfare i fabbisogni di circa 3.000 famiglie.
Area magazzino
L’area destinata a magazzino, che occupa circa il 90% dell’intero corpo di fabbrica, è stata dotata di 33 bocche di carico per l’entrata e di altrettante per l’uscita della merce, attrezzate con pedane elettroidrauliche.
Il magazzino è organizzato in aree funzionali così suddivise: il 50% è destinato allo stoccaggio dei materiali in corridoi attrezzati con scaffalature a gestione automatizzata; il 45% è destinato ad accogliere un’area con presenza di persone (Area Ccp); il restante 5% è adibito a locali tecnici, di collegamento e di manutenzione.
Solaio contro terra
Il fabbricato non presenta locali interrati e la pavimentazione interna, visti i grossi carichi gravitanti sulla pavimentazione del magazzino, non ha previsto l’utilizzo di un vespaio areato.
È stato così realizzato un massetto in calcestruzzo armato con fibre polimeriche strutturali e finitura superficiale con spolvero al quarzo, opportunamente impermeabilizzato grazie all’inserimento di un telo impermeabile a separazione tra lo strato di preparazione e il getto della pavimentazione; quest’ultima dotata di giunti metallici e giunti per il controllo della contrazione.
Alla base di tutto il sedime dell’edificio è stato inoltre steso uno strato in polietilene Ldpe (a bassa densità) come elemento schermante verso il terreno, a protezione di eventuali accumuli di gas Radon.
Stoccaggio del materiale
Nel nuovo polo possono essere lavorati fino a 375.000 pacchi al giorno, spostati lungo 20 km di nastri trasportatori e per mezzo di 675 navette automatiche. Lo stoccaggio della merce denota la conformazione dell’immobile e viene gestita attraverso tre differenti modalità:
- area 1 – carico e scarico e movimentazione merce con presenza di persone: (13,95 m di altezza) la merce viene caricata e scaricata dai camion e indirizzata negli altri comparti per il successivo smistamento attraverso operazioni manuali degli operatori che fanno movimentare la merce su un sistema domotico di rulliere;
- area 2 – Osr Shuttle: (17,96 m di altezza) lo stoccaggio della merce avviene direttamente a una o più profondità attraverso un meccanismo robotizzato. Il sistema è in grado di ordinare le unità di carico in uscita dallo stoccaggio con una perfetta sequenza alle stazioni di lavoro con logica just in time;
- area 3 – Miniload: (26,73 m di altezza) si tratta di un sistema di stoccaggio per contenitori o vassoi che integra in un unico prodotto le scaffalature, i macchinari e il software di gestione magazzini.
È formato da un corridoio centrale dove circola un trasloelevatore e da due scaffalature situate su entrambi i lati per la sistemazione di scatole o vassoi. La zona di automazione e movimentazione è formata da trasportatori nei quali il trasloelevatore deposita il carico estratto dalla scaffalatura.
Tutto il sistema è coordinato da un software di gestione che registra l’ubicazione di tutti i materiali del magazzino e mantiene un inventario in tempo reale. In aggiunta alle aree di cui sopra è presente l’area 4, dedicata a postazioni di gestione locale delle apparecchiature e alla manutenzione.
Impianto elettrico
La distribuzione interna dell’impianto elettrico è stata realizzata mediante canalizzazioni in acciaio zincato con cavi a ridotta formazione di fumi e gas tossici. L’impianto di illuminazione è stato realizzato mediante l’installazione di binari elettrificati Ip55 con il compito di sostenere e alimentare gli apparecchi di illuminazione completi di lampade a Led, munite di ottica concentrante o diffondente a seconda delle necessità.
L’impianto forza motrice è costituito da alcune prese di servizio interbloccate tipo Cee, munite di fusibili di protezione dislocati lungo il perimetro dell’edificio e in prossimità delle baie di carico. Infine, l’impianto di messa a terra è stato realizzato con puntazze e cavo in rame di lunghezza e sezione atte a garantire il rispetto delle normative vigenti.
Impianto di riscaldamento e raffrescamento
È stata prevista la realizzazione di un impianto di raffrescamento e di riscaldamento in una parte del magazzino mediante impianti a espansione diretta a pompa di calore e canali di mandata aria in lamiera di acciaio zincato microforata a sezione circolare.
Questo è stato realizzato tramite dei rooftop con distribuzione interna mediante canalizzazioni flessibili in quanto non è presente il controsoffitto. L’impianto è inoltre integrato con un sistema fotovoltaico posto in copertura.
Impianto antincendio
L’edificio è stato munito di un sistema manuale d’allarme acustico e da un impianto fisso di rilevazione, segnalazione e spegnimento automatici (impianto sprinkler e reti idranti).
L’impianto a protezione dell’insediamento utilizza la rete idrica di spegnimento costituita da 2 riserve idriche (composte da 2 serbatoi cilindrici verticali in lamiera zincata), 2 stazioni di pompaggio, una rete di distribuzione unica ad anello per la rete idranti, da idranti Uni 70 soprassuolo e sottosuolo e da Uni 45 bocche di presa a parete.
Corpo uffici
Gli uffici, gli spogliatoi e i relativi locali di servizio sono localizzati al piano terra e al piano primo, con ingresso dal fronte nord e collegati al magazzino tramite porte EI120.
Vespaio areato
La pavimentazione dei locali posti al piano terra è stata realizzata con materiale impermeabile e resistente, isolata dal terreno mediante un vespaio areato per evitare la risalita dell’umidità. Quest’ultimo è stato realizzato con igloo di altezza 45 cm, sormontato da un telo in Pvc, dei pannelli isolanti in polistirene estruso, un sottofondo e la pavimentazione in gres porcellanato o Pvc.
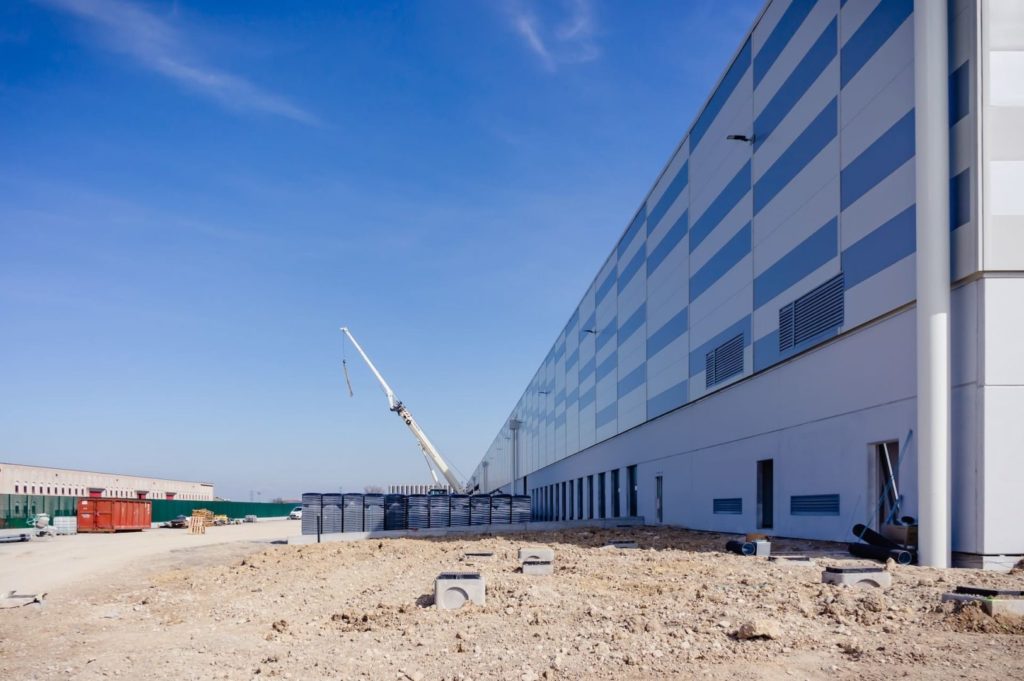
Pareti interne e controsoffitti
Le pareti interne sono state realizzate in cartongesso prodotte da Knauf, diversificate in base alle zone dell’edificio: è stato utilizzato un cartongesso idrorepellente per quanto riguarda bagni e spogliatoi, un cartongesso standard per gli uffici e un cartongesso Rei per la separazione del blocco uffici dal magazzino. È stato inoltre realizzato un controsoffitto con pannelli da 60×60 cm in fibra minerale a foratura irregolare.
Impianto elettrico
Le aperture dell’edificio sono state dimensionate in modo tale da garantire un corretto apporto aero illuminante; la luce naturale è stata poi integrata con quella artificiale (lampade fluorescenti con ottica lamellare), modulabile in base all’organizzazione degli spazi interni, alla loro destinazione d’uso e al loro livello di occupazione (500 lux nei locali uffici e 200 lux locali di servizio e tecnologici).
La componente impiantistica è stata quindi utilizzata a integrazione dell’apporto naturale di luce attraverso l’istallazione di sensori che consentono la regolazione locale del benessere degli ambienti interni. L’impianto di messa a terra è stato collegato al dispersore disposto ad anello intorno al fabbricato mediante conduttore di rame nudo.
Climatizzazione
L’impianto di riscaldamento e di raffrescamento consiste in un sistema ad espansione diretta con gas ecologico R410A a portata variabile con funzionamento a pompa di calore in modo che tutti i locali siano autonomamente gestiti e controllati in termini di temperatura.
Le unità esterne sono state installate sulla copertura del corpo uffici mentre quelle interne a cassetta sono state installate nel controsoffitto. L’acqua calda per uso domestico a servizio degli spogliatoi e dei bagni è fornita con impianto a pompa di calore, con recuperatore posto sulla copertura degli uffici ed integrato con un sistema a pannelli solari e fotovoltaici.
Impianto idrico
L’impianto idrico sanitario è gestito in maniera tale da controllare e contenere i consumi di acqua. Ogni punto acqua infatti è stato collegato, mediante elettrovalvola, a un sensore di presenza che consente di evitare sprechi chiudendo l’adduzione di acqua qualora venissero lasciati rubinetti aperti.
Opere esterne
Le aree esterne del progetto comprendono la viabilità e le aree di manovra, le aree di parcheggio auto e camion, il piazzale di carico, le aree a verde, il percorso vita e i campi sportivi, il bacino di laminazione e i locali a uso tecnico, per un totale di 145.000 mq.
Pavimentazione esterna
- La scelta del tipo di pavimentazione è stata gestita in maniera differente a seconda della destinazione d’uso dell’area esterna, in particolare: per le aree a parcheggio sono stati utilizzati autobloccanti con superficie riflettente a 3 anni pari a 35 al fine di mitigare l’effetto isola di calore;
- per le aree antistanti le baie di carico è stata realizzata una pavimentazione in battuto di cemento (non è stato possibile utilizzare gli autobloccanti a causa dell’elevato peso dei mezzi ivi circolanti);
- per tutti gli altri spazi (piazzali esterni, strade di accesso, parcheggi) è stato posato un manto bituminoso.
Aree verdi
Le aree verdi, che occupano circa 80.000 mq di superficie sterna, sono state piantumate con specie arboree tipiche del luogo che non necessitano di particolare manutenzione, atte a mitigare l’impatto ecologico dell’intervento. Gli spazi esterni sono stati inoltre corredati da aree utili a favorire l’aggregazione dei dipendenti, quali campetti da calcetto, percorso vita, deposito biciclette e sedute/tavoli.
Illuminazione
L’illuminazione esterna al fabbricato ha previsto l’installazione di lampade poste sulla facciata dell’edificio, mentre per i parcheggi e per le strade di accesso sono stati utilizzati dei lampioni stradali.
Gestione delle acque
Il progetto ha previsto la realizzazione di un sistema di raccolta delle acque di piattaforma della viabilità e dei piazzali interni. In particolare, per la raccolta delle acque dei piazzali sono state utilizzate caditoie stradali con chiusino in ghisa e griglie, oltre a pozzetti di ispezione distribuiti uniformemente lungo la rete.
Le acque nere sono state convogliate nell’apposito collettore comunale. Non sono stati previsti scarichi derivanti da lavorazioni industriali dato che i reflui scaricati sono tutti di tipo civile.
Per la gestione di tutte le altre utenze quali acqua potabile, energia elettrica, trasmissione dati e telefonia, l’immobile è stato dotato di polifore opportunamente dimensionate, ovvero cavidotti di dimensioni idonei e relativi pozzetti di ispezione, condutture in Ped per acqua potabile.
Nelle aree esterne è stato inoltre collocato il bacino di laminazione necessario per il rispetto del principio di invarianza idraulica. Lo scopo di tale bacino è quello di garantire l’accumulo temporaneo delle acque meteoriche all’interno dell’area, per poi smaltirle.
Essendo il bacino di grandi dimensioni e collocato a elevata profondità, è stato necessario effettuare degli scavi importanti, realizzare delle scarpate adeguatamente dimensionate e installare una recinzione di 2 metri di altezza per garantirne la sicurezza.
Il sistema bacacier
Il sistema Bacacier è il sistema a copertura piana indicato per la costruzione di prefabbricati a uso logistico. Questo sistema costruttivo è realizzato con travi in c.ap. a sezione a “I” e di elementi arcarecci in c.a.p. a sezione a “T” quali elementi “secondari”.
La struttura in calcestruzzo viene completata con l’applicazione di una lamiera grecata posata sopra gli arcarecci a “T”, dando una leggera pendenza verso l’esterno dell’edificio per consentire il corretto deflusso delle acque meteoriche.
La coibentazione e l’impermeabilizzazione è realizzata con l’impiego di un pannello isolante (polistirene o lana minerale) e membrana bituminosa o sintetica (Tpo) con caratteristiche adattabili alle diverse esigenze termiche e per la resistenza al fuoco (Broof). Il sistema a copertura piana Bacacier può essere dotato di aperture per lucernari/Efc supportate da barelle in calcestruzzo, basamenti in lamiera, rete anticaduta.
I criteri esg e la certificazione leed
La progettazione del parco logistico ha seguito i criteri Esg (“Environmental”, “Social” and “Governance” – indicatori che permettono di analizzare l’attività di un’impresa non solo su aspetti finanziari, ma anche sotto il profilo ambientale, sociale e di buona governance adottando come proprio il concetto di sviluppo sostenibile.
Una progettazione quindi mirata all’impatto ambientale del building, al suo carico di Ghg (emissioni di gas serra), all’efficientamento energetico e al contenimento dei consumi; una progettazione che ha tenuto conto anche della componente umanistica (impatto sulla comunità locale, condizioni lavorative, salute e sicurezza) e di quella economica (interessi collettivi, compenso esecutivo e contenimento delle spese).
Tali obiettivi sono in linea con quelli perseguiti dai protocolli internazionali di certificazione su base volontaria. Per tale motivo l’edificio è stato realizzato seguendo quanto stabilito dal protocollo Leed Gold che promuove edifici sostenibili e aree territoriali ad alte prestazioni attraverso un sistema di progettazione integrata. I temi cardini, seguiti già dalla fase preliminare del progetto, sono stati:
- comfort ambientale: il benessere degli spazi interni è controllato attraverso la definizione di standard minimi, quali il controllo della portata d’aria, il monitoraggio della quantità di anidride carbonica presente, la prevenzione da contaminazione e l’utilizzo di materiali di finitura che contengano una concentrazione di contaminanti chimici (Voc, Pm10, formaldeide) ridotta.
- energia: progettazione, costruzione e gestione dell’edificio sono stati supportati da un energy modelling, sistema che calcola l’efficienza energetica dell’edificio, puntando a un miglioramento in riferimento alla normativa nazionale. Parte della richiesta di energia elettrica è stata compensata da quella prodotta in copertura dai pannelli fotovoltaici (80%), la restante viene ricevuta dalla rete nazionale. L’intero sistema impiantistico viene gestito tramite il sistema Bms (Building Management Systems), un sistema di gestione dell’edificio che consente di monitorare e controllare i servizi quali riscaldamento, ventilazione e condizionamento d’aria e di garantire che questi funzionino ai massimi livelli di efficienza e risparmio;
- gestione delle acque: sono state inserite delle vasche di accumulo
- dell’acqua piovana per il suo riutilizzo nell’irrigazione delle aree verdi e un sistema di gestione dell’impianto idrico sanitario interno;
- materiali: la scelta dei materiali ha prediletto la produzione a km 0, la sottoscrizione di contratti d’appalto con imprese locali e il contenimento/riciclo nella produzione di rifiuti e materiali di risulta;
- ambiente: particolare attenzione è stata posta alla scelta delle specie arboree e all’inserimento di aree attrezzate per i dipendenti nelle aree esterne;
- effetto isola di calore: le strategie utilizzate per la riduzione di questo effetto (fenomeno per cui si registra un incremento di temperatura nell’area che interessa il nuovo insediamento) hanno riguardato l’inserimento di aree vegetali in sostituzione delle superfici impermeabili che assorbono calore, l’utilizzo di pavimentazioni autobloccanti, di pannelli fotovoltaici e l’utilizzo di materiali con colorazioni chiare;
- superfici riflettenti e Sri: sono stati scelti materiali di copertura e per le aree esterne con Sri e Sr particolarmente performanti e sono state realizzare aree ombreggiate naturalmente e artificialmente, rispettando i paramenti minimi richiesti dal protocollo di sostenibilità Leed;
- gestione del cantiere: è stato implementato un piano di controllo dell’erosione-sedimentazione. Le attività da costruzione hanno previsto quindi: la costruzione di un sistema manuale di lavaggio delle ruote degli autocarri e un sistema di raccolta, filtraggio e smaltimento delle acque, l’utilizzo di container ermetici con funzione di vasca temporanea di lavaggio della canala betoniere, l’installazione di recinzioni esterne perimetrali, l’installazione di protezioni filtranti come tessuto non tessuto su tutte le caditoie attive, l’impiego di un serbatoio di raccolta e di riutilizzo dell’acqua.
L’intervento ha prediletto quindi un approccio innovativo, dalla progettazione, al cantiere, fino alla messa in esercizio: l’edificio non è stato più analizzato esclusivamente sul piano del consumo energetico, ma per il suo intero ciclo di vita. Questa filosofia si è quindi tradotta in una strategia progettuale: il protocollo di sostenibilità Leed, nel suo livello massimo raggiungibile, il Leed Gold.
Superficie riflettente e Sri
La natura e il colore dei materiali con cui sono costruiti gli edifici influenzano l’effetto isola di calore. I parametri utilizzati per valutare il contributo dei materiali all’effetto “isola di calore” sono l’Indice di Riflettanza Solare (Sri) e la Riflettanza Solare (Sr). La misura più efficace della capacità di un materiale di copertura di respingere il calore solare è l’indice di riflettanza solare (Sri).
Per misurare la reiezione del calore solare di componenti che non sono materiali di copertura, per esempio, vegetazione, dispositivi di ombreggiamento e altri componenti meno riflettenti viene utilizzata la riflettanza solare (Sr). Sr è un modo più appropriato per misurare i materiali diversi dal tetto, che hanno una massa termica maggiore.
Oltre al valore Sri o Sr iniziali, ovvero al momento in cui vengono posati in cantiere, la scelta dei materiali tiene conto dei valori Sri o Sr dopo tre anni dalla posa del prodotto, misurando quindi le prestazioni dei materiali nel tempo.
di Valentina Puglisi
La scheda
Committente: Logiman
Project e construction managment: Engineering2k
Progettista architettonico: SFRE
Bim managment: AI Engineering
General contractor: Engineering2k
Direzione lavori: Carlo Scotti
Direzione lavori antincendio: SFRE – Service For Real Estate
Baie di carico: Hoermann
Struttura portante: Isocell
Cartongessi: Knauf