Efficiente, flessibile, sostenibile e non solo sotto il profilo ambientale: è questa l’edilizia del futuro. A patto di evolvere e puntare all’industrializzazione, ossia alla metodologia off-site per cui si producono in fabbrica elementi costruttivi, per esempio pilastri e travi, da assemblare successivamente in loco.
Delle tecnologie disponibili e dei vantaggi si è discusso nel convegno Costruiamo il futuro, organizzato da una cordata di imprese italiane, come opportunità di confronto tra investitori, produttori, progettisti: «Riteniamo che oramai l’industrializzazione off-site sia l’unica strada percorribile per ridurre l’impatto ambientale nelle nostre città. Si tratta di una via reale alla sostenibilità di tutto il comparto, non solo per quanto riguarda le nuove costruzioni ma anche per la riqualificazione e riconversione di aree dismesse e vetuste», ha dichiarato Franco Daniele, presidente di Tecnostrutture, una delle aziende capofila dell’iniziativa. Già, perché il settore, afflitto da tempo da problemi come la scarsità di manodopera specializzata, l’anzianità del parco immobiliare, i tempi lunghi di realizzazione, fino all’incertezza e alla fluttuazione dei prezzi che non garantiscono costi certi, richiede un cambio di metodologia. Ed è urgente.
Per questo nel corso del convegno sono stati presentati quattro progetti di successo, che illustrano concretamente come questo approccio possa rendere più sostenibile il comparto, grazie alla sua capacità di ottimizzare le risorse e rispondere ai criteri Esg, di diminuire la durata dei lavori, di contenere gli aumenti nei preventivi, di tutelare la sicurezza e il benessere dei manovali.
«Dopo la forte spinta verso la prefabbricazione che ha caratterizzato il secondo dopoguerra, all’evoluzione tecnologica dei sistemi di costruzione off-site non ha corrisposto la diffusione che questi meriterebbero, considerati gli indubbi vantaggi che presentano rispetto alla costruzione on-site», ha spiegato Eugenio Kannes, amministratore delegato di Brioschi Sviluppo Immobiliare.
Che ha aggiunto: «Ma oggi la compresenza di diversi fattori può favorire il progressivo trasferimento della produzione dal cantiere alla fabbrica: la digitalizzazione del settore e in particolare la diffusione del Bim, la crescente attenzione agli aspetti ambientali e ai criteri Esg, la carenza di manodopera qualificata e l’aumento dei costi di costruzione, che dal 2019 a oggi, complice la pandemia e le guerre, sono lievitati del 30%, spingono verso la ricerca di soluzioni alternative a quelle tradizionali».
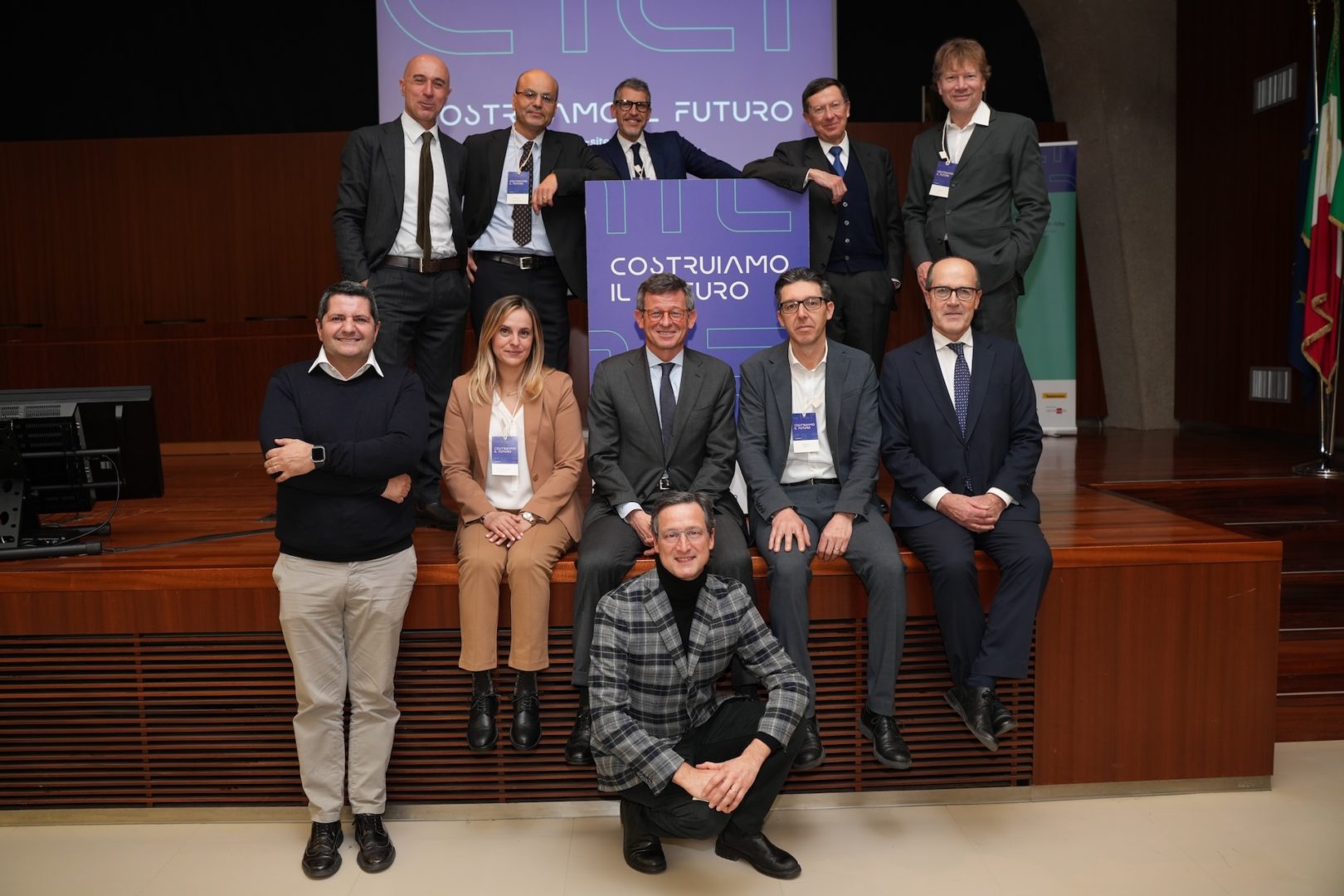
Tecnologia off-site Nps di Tecnostrutture
Il villaggio olimpico è stato realizzato a tempo record proprio ricorrendo alla tecnologia off-site Nps (New Performance System) sviluppata da Tecnostrutture, azienda veneta specializzata in prefabbricati a struttura mista acciaio-calcestruzzo. Situato nell’area sud-ovest dello scalo di Porta Romana di Milano e destinato ad accogliere gli atleti delle Olimpiadi Invernali 2026, il progetto è stato completato in soli 12 mesi, che equivale a una riduzione dei tempi di realizzazione del 40% circa rispetto a un approccio tradizionale.
Infatti, uno dei fattori di successo è stata la prefabbricazione di tipo leggero proposta da Tecnostrutture: pilastri, travi, solai e rampe scala, in materiale sostenibile, prodotti in stabilimento e assemblati in cantiere. Risultato? I sei edifici, da otto piani ciascuno, con una superficie media di 900 metri quadri per piano per un totale di 46mila metri quadrati, sono tutti certificati Leed e, alle strutture edilizie permanenti di quello che diventerà più grande studentato d’Italia, con circa 1.700 posti letto su una superficie di 47mila metri quadrati, sono state integrate con soluzioni temporanee riutilizzabili.
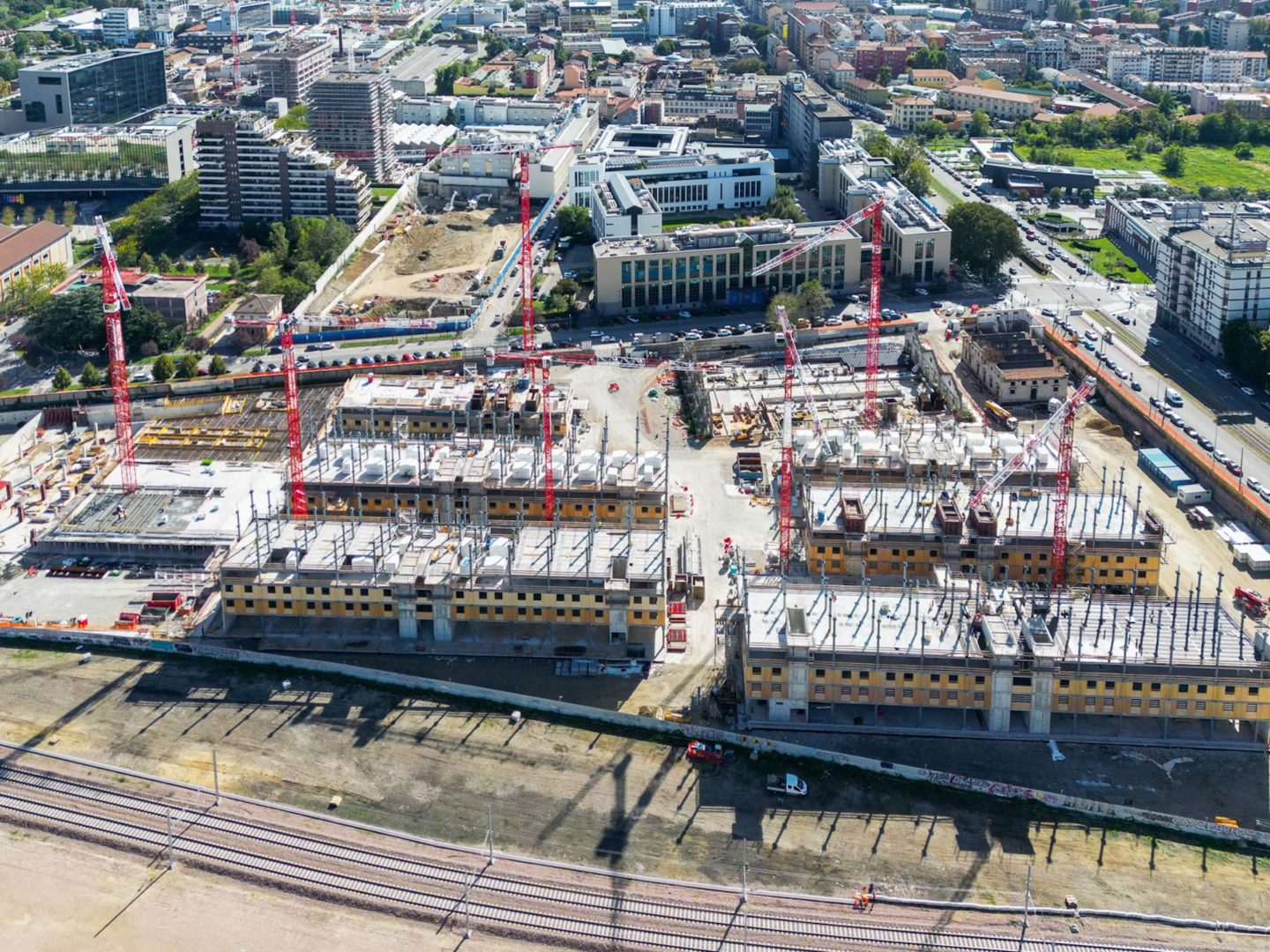
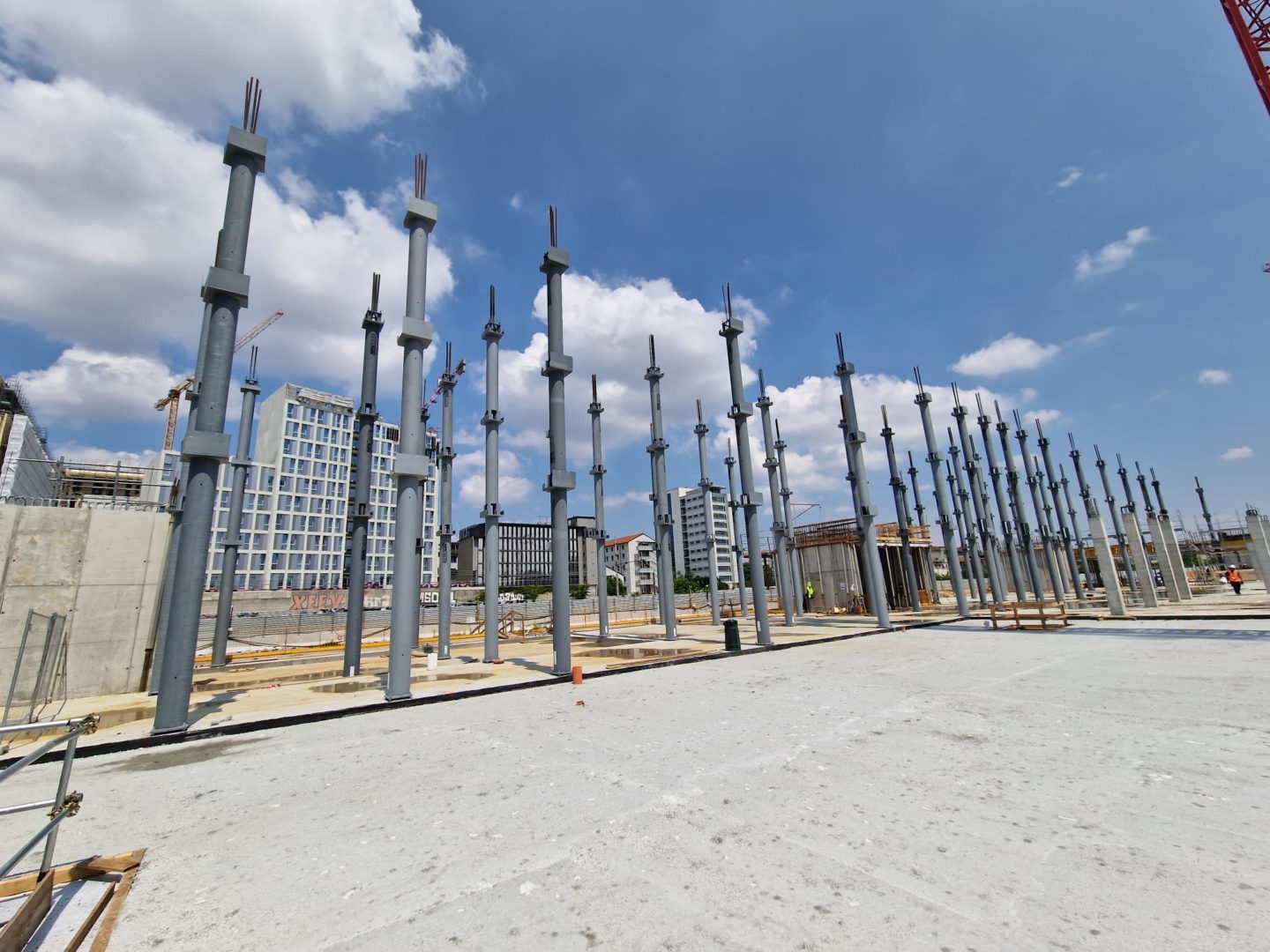
Un percorso a tappe
Costruire a Milano impone limiti di cantiere e i vincoli logistici, per superare questi ostacoli il lavoro è stato suddiviso in fasi: il 4 gennaio 2023 è stata presentata la soluzione tecnica, il 9 febbraio 2023 la firma del contratto a cui è seguita la progettazione Bim, entro il 18 aprile la realizzazione di tutte strutture industrializzate e, il 5 giugno la posa del primo pilastro monopiano.
Tempi rapidissimi si diceva, infatti al posto di puntelli e casseri che nell’edilizia tradizionale in fase di scasseratura limitano l’operatività del cantiere, con gli elementi prefabbricati di Tecnostrutture l’accesso agli spazi liberi e alle sezioni compatte è immediato, grazie al sistema Nps che sfrutta l’efficienza strutturale di acciaio e calcestruzzo per ottenere performance strutturali tali da consentire il montaggio in autoportanza.
Tra i diversi elementi, tutti certificati Cee ed Epd (Environmental Product Declaration) i pilastri presentano sezioni in acciaio e un nucleo interno in calcestruzzo, mentre le travi sono realizzate con una struttura tralicciata in acciaio, di cui il 90% è riciclato. Insomma, in appena sette mesi e con solo nove operai e tre gru, l’impresa appaltatrice ha completato gli otto piani dei sei edifici sovrapponendo le diverse fasi lavorative, un approccio di ottimizzazione dei processi che ha mantenuto il cantiere pulito, ordinato.
I vantaggi
In pratica, sostengono in Tecnostrutture, le operazioni cruciali sono state eseguite fuori del cantiere mentre l’assemblaggio successivo e in loco ha permesso di sfruttare pienamente gli spazi interni: per esempio, mentre al piano inferiore venivano completate le tamponature interne e venivano posati i bagni, al piano superiore si procedeva con l’installazione del solaio, senza interferenze tra le due lavorazioni. Inoltre, il sistema Nps ha ridotto dell’80% il fabbisogno di manodopera in cantiere, semplificando anche la gestione del personale.
Dunque, alla maggiore efficienza in termini di sicurezza si aggiunge un impatto ambientale più contenuto: pilastri, travi e i solai sono stati consegnati solo al momento della posa, eliminando la necessità di aree di stoccaggio, dettaglio particolarmente rilevante nel perimetro di un cantiere. Non solo, senza l’impiego di materiali provvisori sono stati risparmiati circa 160 viaggi tra andata e ritorno per spostare le attrezzature, generando un impatto positivo sia dal punto di vista economico che ambientale. Una metodologia, quella della scomposizione dell’opera edilizia nei suoi elementi principali da realizzare in fabbrica, che ha consentito di anticipare tempi di ben tre mesi sul completamento del progetto. Insomma, un vero successo. Olimpico.
Rubner mette radici ad Amburgo
Si staglia per 72 metri su 20 piani, di cui 16 in legno: Roots è l’edificio residenziale costruito in questo materiale più alto della Germania e si trova ad HafenCity, il quartiere portuale di Amburgo, dove la municipalità prevede 12 mila nuovi abitanti e 40 mila posti di lavoro entro il 2027.
L’aspetto più interessante è che si tratta di un fabbricato ibrido, per cui il piano interrato e il piano terra sono in cemento armato, mentre quelli superiori sono in legno, appunto, e rappresenta un esempio tangibile delle conoscenze, delle capacità e delle tecnologie disponibili per realizzare strutture di qualità, in tempi brevi, a costi certi e anche con una maggiore attenzione all’ambiente.
La torre e la struttura a fianco di sette piani, sono state progettate dallo studio di architettura Störmer, Murphy and Partner, con la consulenza di Rubner, azienda altoatesina specializzata in ingegneria edile in legno, che ha fornito il suo contribuito sia in fase di progettazione sia nell’esecuzione tecnica e strutturale. L’edificio principale ospita circa 128 appartamenti di proprietà tra bilocali, trilocali, quadrilocali, mentre quello laterale offre 53 unità abitative a canone agevolato per una superficie complessiva di oltre 20 mila metri quadrati.
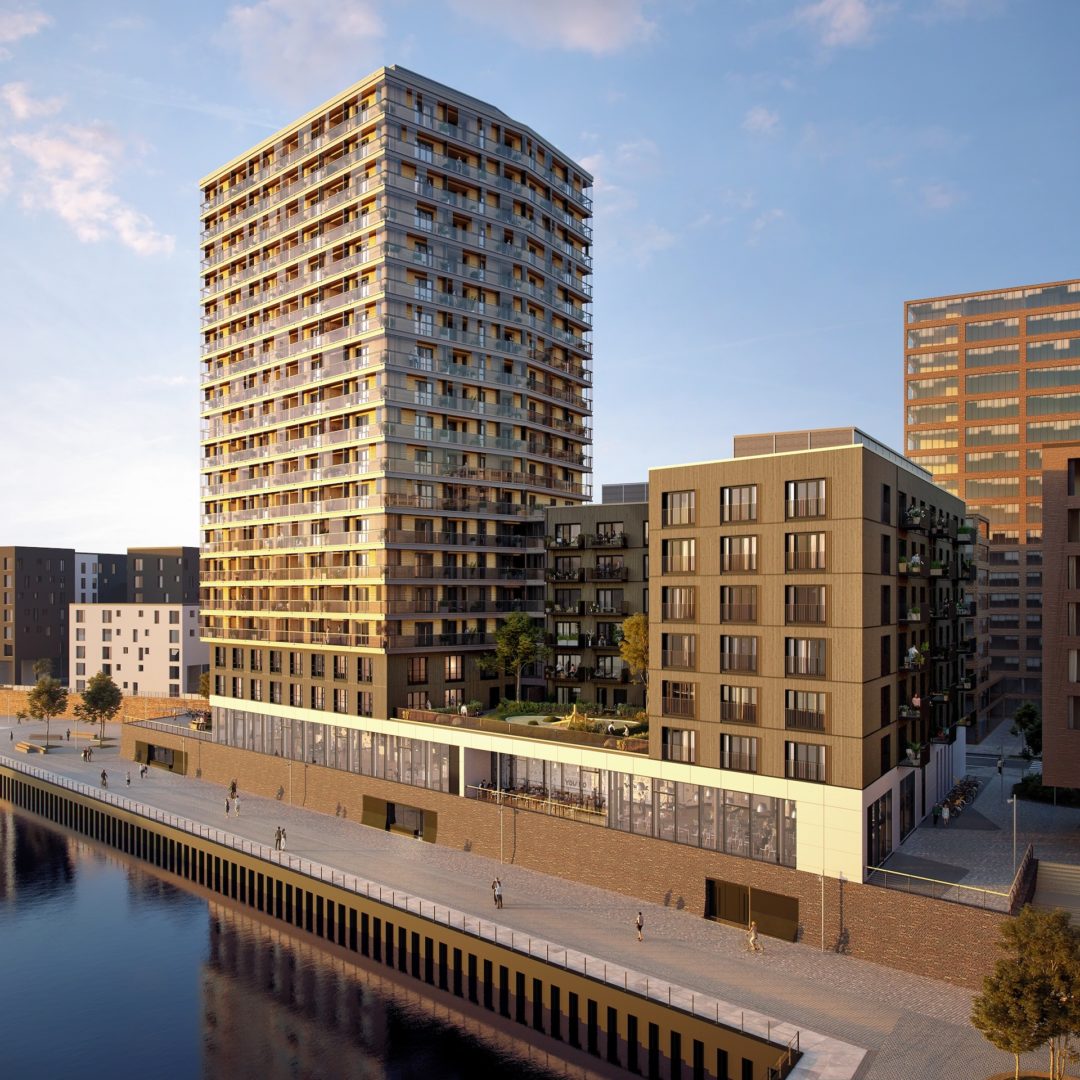
Quando la materia è l’opera
Rubner ha fornito le pareti esterne prefabbricate e i soffitti in legno massiccio, insieme a un anello portante della parete interna, elementi che costituiscono la struttura principale della torre e coprono una superficie di 16.200 metri quadrati. Inoltre, i pannelli X-Lam da 240-280 millimetri di spessore nei soffitti, insieme a una seconda facciata in vetro installata in loco, garantiscono protezione antincendio, dai raggi Uv e dall’umidità.
In totale sono stati utilizzati oltre 5.500 metri cubi di legno di conifera, un volume che consente di risparmiare circa 26 mila tonnellate di biossido di carbonio, rispetto alle costruzioni convenzionali. Completata in soli 16 mesi, dal maggio 2022 all’agosto 2023, grazie anche alla semplificazione delle opere di fondazione, realizzate su pali più piccoli e leggeri rispetto alle fondazioni in cemento o acciaio di edifici simili, un dimensionare fondazioni, risparmiando spazio, risorse e costi.
Ma attenzione, questa leggerezza è stata ottenuta in fase di progettazione con il coinvolgimento di tutti i soggetti interessati e si è concentrata su aspetti cruciali come le prestazioni energetiche, acustiche e la resistenza al fuoco, inizialmente prevista di 120 minuti, ridotta in seguito a 90, senza compromettere la solidità strutturale in quanto ibrida, con un nucleo centrale in cemento armato.
L’intervento
Le strutture portanti in legno si estendono lungo il perimetro dell’edificio e seguono una linea definita internamente, dove vengono posizionati gli elementi prefabbricati, si tratta di pareti portanti esterne e interne prefabbricate in legno, i solai sono realizzati con pannelli in legno lamellare incrociato, mentre tutte le altre pareti sono realizzate a secco con tecnologia nota come cartongesso. Scelta che permette una grande flessibilità degli spazi abitativi e la possibilità di rimodulare gli appartamenti in base alle future esigenze.
Non solo, durante la progettazione delle componenti prefabbricate, la stessa importanza data alla tecnologia di assemblaggio è stata conferita alla possibilità di smontaggio con un duplice obiettivo: consentire la separazione dei singoli elementi al termine del ciclo di vita dell’edificio oppure abilitare una diversa destinazione d’uso, magari cambiando la facciata.
La modellazione B è stata utilizzata non solo per trasferire i dati dalla fase di progettazione alla produzione degli elementi prefabbricati, ma anche per pianificare l’intervento in cantiere, simulando le diverse fasi di assemblaggio e ottimizzando l’utilizzo delle gru. Complessivamente, il montaggio di un piano ha richiesto meno di tre settimane, coinvolgendo 53 elementi di parete e 53 elementi di solaio.
Due è meglio di uno
In Rubner ne sono convinti, con l’edilizia off-site il concetto tradizionale di cantiere è superato: sono invece due distinte fasi lavorative che procedono in parallelo. Da un lato, c’è il cantiere tradizionale sul sito di costruzione; dall’altro, c’è quello nello stabilimento di fabbricazione ed è qui che si concentrano molte delle attività, dove vengono realizzati intere componenti come pareti complete di infissi, serramenti e rivestimenti esterni.
Una volta completati, questi elementi vengono trasportati sul cantiere e installati direttamente. Addirittura, come nel caso di una parete esterna prefabbricata, di oltre sei tonnellate e lunga 14 metri, possono essere sollevati direttamente dal mezzo di trasporto e collocati nella loro posizione finale senza ulteriori operazioni. Certo, non è semplice, ci vuole la tecnologia adeguata, ma Roots è la dimostrazione che si può fare.
Campus Milano Internazionale Pichler Projects
Chi sostiene che un’estetica di qualità non sia compatibile con l’edilizia off-site non ha visto il progetto curato da GaS Architects – Goring & Straja Studio in collaborazione con Pichler Projects, azienda con sede a Bolzano specializzata nella progettazione e realizzazione di strutture in acciaio e facciate, che ha costruito chiavi in mano, un edificio multipiano commissionato dalla società di sviluppo immobiliare InvestiRE.
Inizialmente concepito come un’opera tradizionale, lo studentato dell’area universitaria Bicocca con i suoi 460 posti letto, spazi comuni, aree aggregative, fitness, mense e cucine è stato completamente rivisto in termini industriali e di prefabbricati. Obiettivo? Renderlo disponibile in un anno e mezzo, giusto in tempo per l’inizio dell’anno accademico a settembre.
Si tratta di una torre residenziale di 15 piani fuori terra, caratterizzata da un’alternanza tra facciate vetrate tamponate con vetri di quattro diverse colorazioni e rivestimenti metallici di colore bianco, il cui nucleo centrale è in calcestruzzo in opera prefabbricato, mentre tutto il resto è stato realizzato con colonne e travi in acciaio e solai di tipo slim floor.
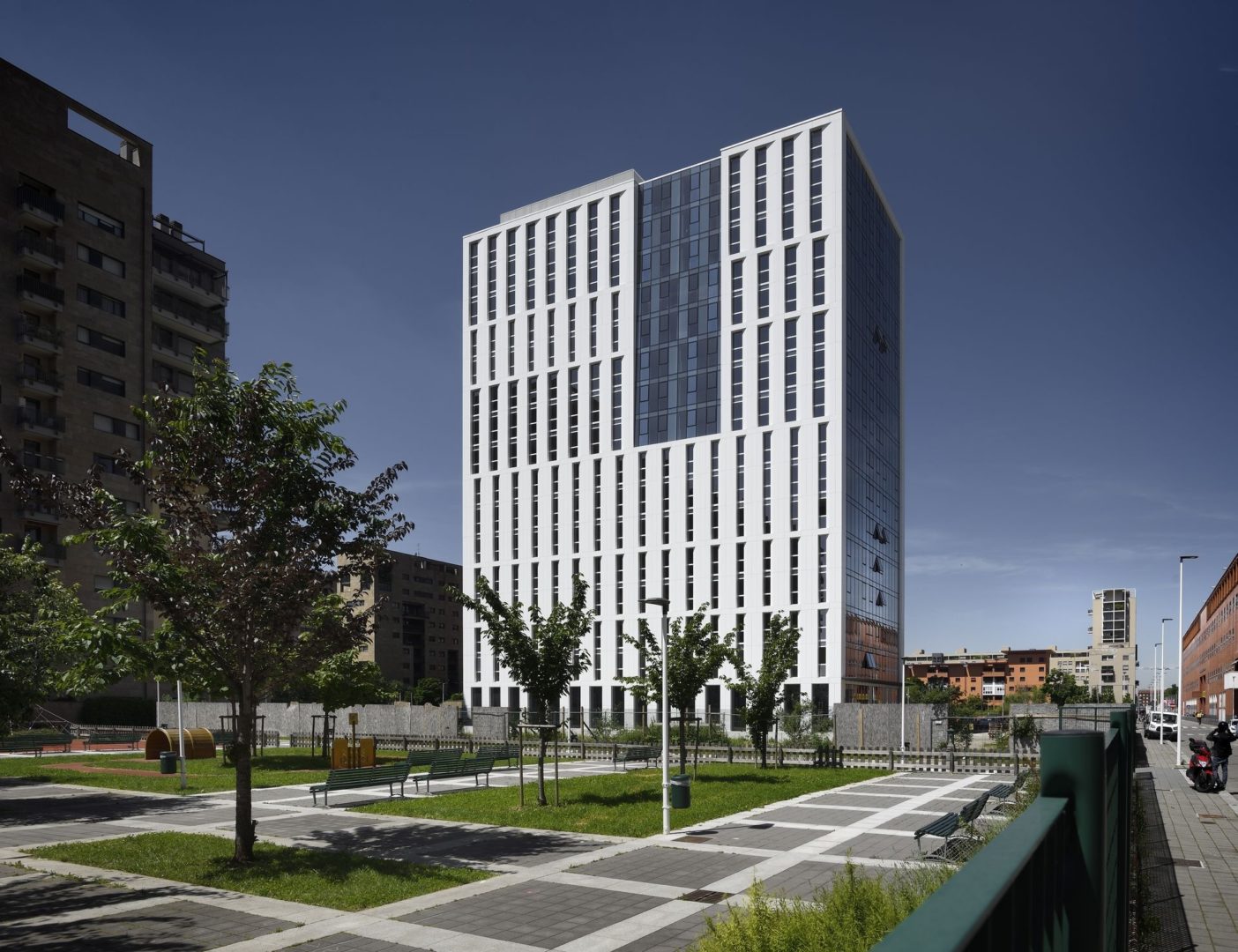
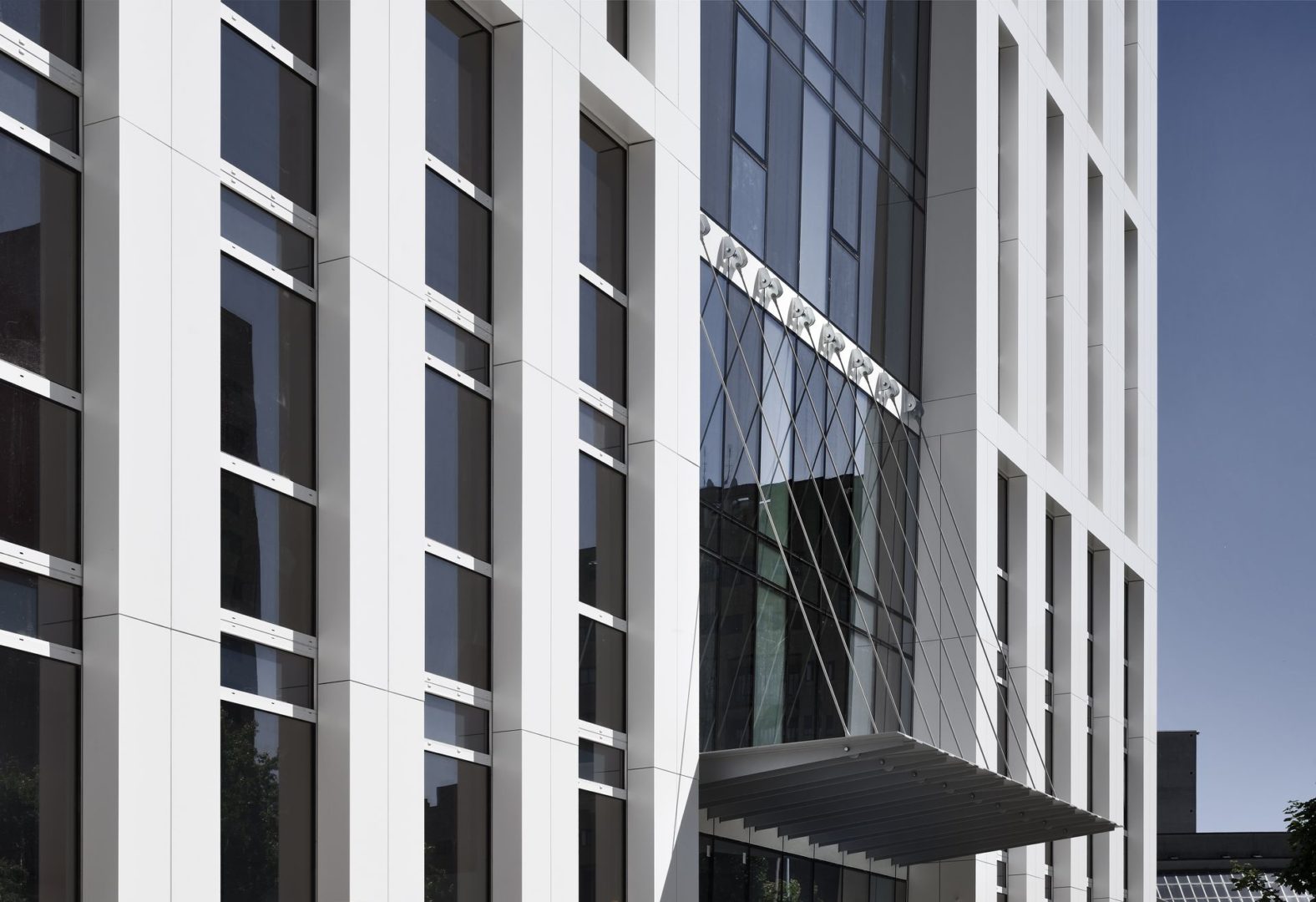
Questa soluzione ha permesso di eliminare completamente le colonne interne dell’edificio, aumentando così la superficie utilizzabile e garantendo una maggiore flessibilità negli spazi interni. Inoltre, le travi metalliche integrate direttamente nel solaio di piano hanno minimizzato la necessità di protezione antincendio.
I tempi di costruzione sono stati rapidi grazie alla sovrapposizione delle diverse fasi di lavoro e alla gestione separata delle diverse attività, da quelle strutturali alle finiture esterne e interne, fino all’impiantistica, garantendo così anche un elevato livello di sicurezza in cantiere. Sebbene la realizzazione dei nuclei in cemento armato sia avvenuta in loco, è stato adottato un approccio industrializzato grazie all’utilizzo di casseri rampanti.
Il piano costruttivo adottato prevedeva il nucleo in calcestruzzo sempre di tre piani in anticipo rispetto alla parte a secco in acciaio, con gli elementi di impalcato prefabbricati in calcestruzzo utilizzando il sistema Slim floor, per ridurre l’altezza strutturale e la protezione dell’elemento in acciaio per quanto riguarda l’esistenza al fuoco. Anche le componenti della facciata sono state completamente industrializzate e prefabbricate.
Tutti i dettagli esecutivi e costruttivi derivano dal modello Bim dell’intero edificio, fino ai file macchina per la posizione dei singoli elementi. 550 le tonnellate di acciaio impiegate per la struttura portante dell’edificio, che presenta una facciata di circa 6 metri quadrati.
Lo studio condotto insieme al project management della committenza ha permesso di comprimere i tempi di costruzione, consentendo di completare un solaio a secco in una settimana e di concludere tre piani in cinque settimane grazie ai getti integrativi.
Per questo, in Pichler Projects sono convinti che un processo costruttivo innovativo come la tecnologia offsite non banalizzi il progetto architettonico, ma anzi permetta un maggiore controllo e una maggiore fedeltà alla visione originale. Tutto naturalmente in isocosto, assicurano in azienda.
262 5th Avenue, New York Gualini
Sarà anche un po’ italiano uno tra i primi dieci grattacieli più alti di tutta Manhattan. È il progetto 262 5th Avenue di New York che riguarda un grattacielo di oltre 270 metri con 56 piani di appartamenti residenziali più sei piani di struttura panoramica sulla sommità. Gualini (controllata del Gruppo Costim), azienda con sede a Bergamo specializzata nel settore dell’involucro edilizio, ha curato la progettazione architettonica e ingegneristica delle facciate strutturali e dei due rivestimenti architettonici.
Questi ultimi, infatti, hanno due anime: una in mattoni in alluminio estruso, un tipo di rivestimento di particolare fattura, molto luminoso; l’altra, maggiormente tecnologica, è in alluminio composito e vetro fotovoltaico, per l’autoproduzione di energia.
Le cellule vetrate sono molto ampie: sono state realizzate direttamente e interamente in Italia per poi essere trasportate con container al porto di New York e da qui al cantiere per l’assemblaggio e il montaggio. Tutta la struttura è personalizzata a seconda delle esigenze del cliente e dell’architetto.
L’involucro
L’opera, attualmente in fase di edificazione, prevede diverse tipologie di facciate: la parte principale sarà a cellule, non ancora installate, da un altro lato ci sarà quella fotovoltaica caratterizzata da diversi brevetti. L’azienda fornirà anche serramenti circolari e rivestimento in composito.
Infatti, il progetto contempla una differenza strutturale tra le facciate orientali, in alluminio e vetro, e quelle a nord e a sud, formate da un sistema sovradimensionato in alluminio e triplo vetro. L’edificio ha un nucleo in cemento armato, caratterizzato da ascensori, scale di uscita, che permetterà agli appartamenti di avere piani open-floor personalizzabili, con ampie zone affacciate sul panorama della città.
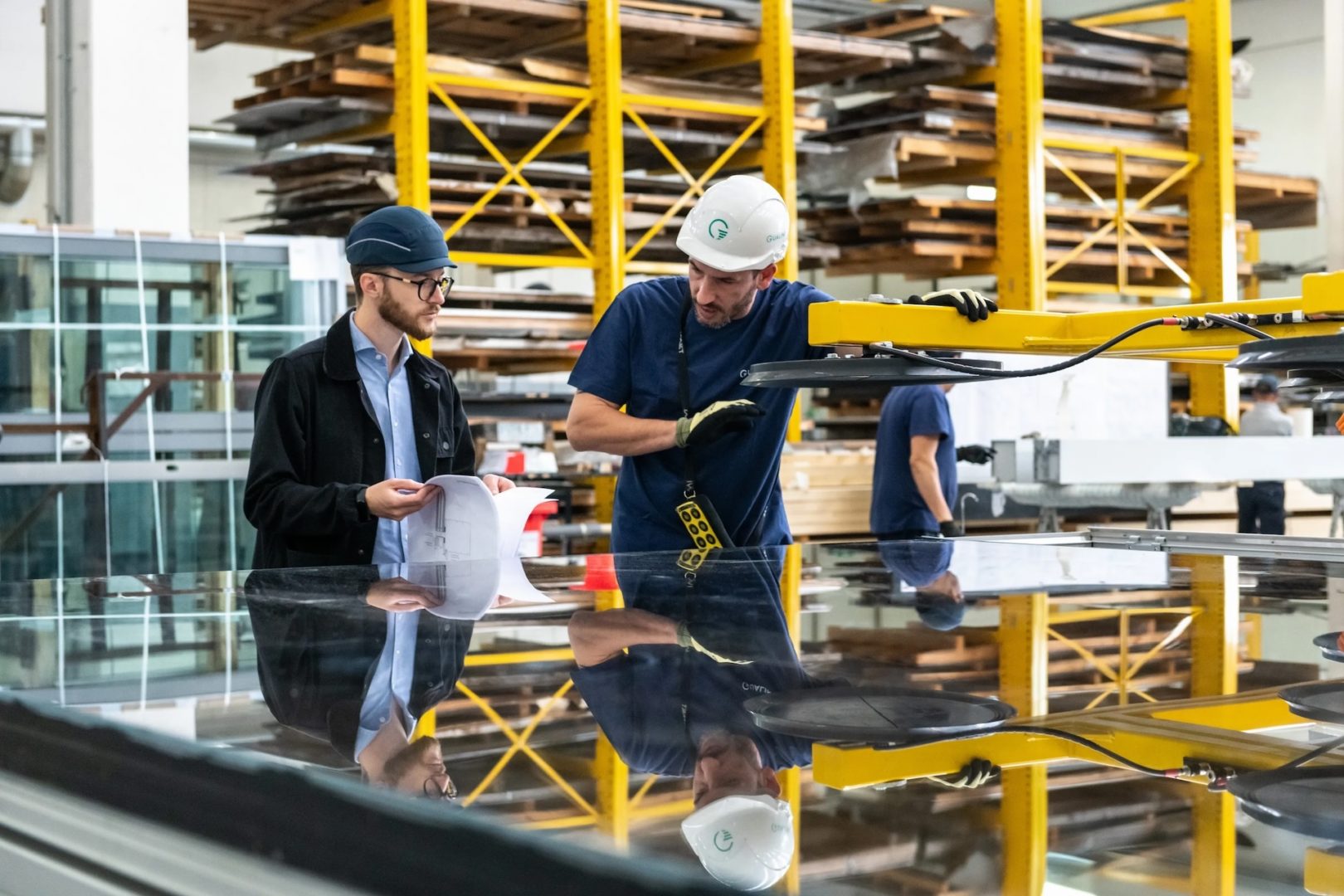
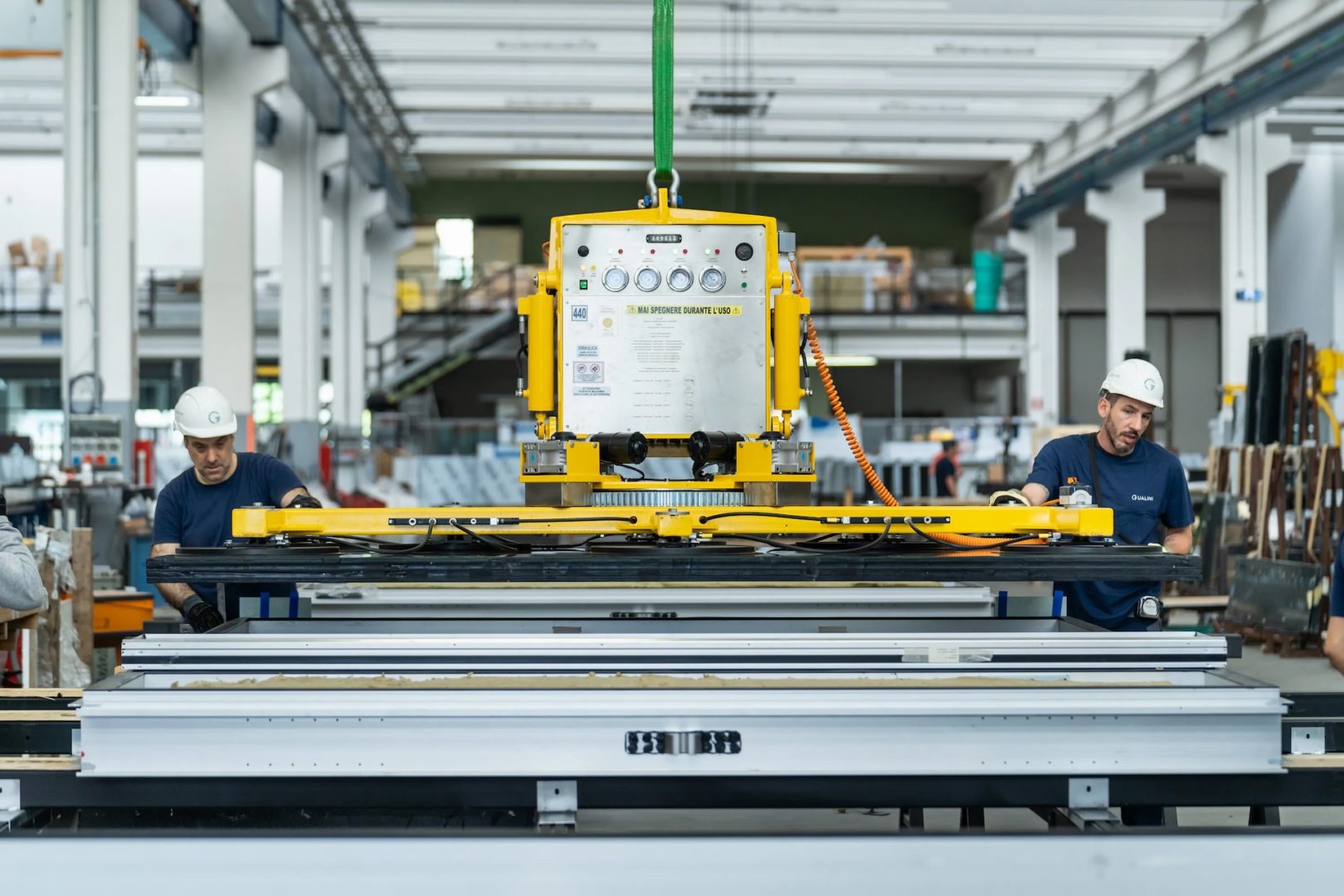
Ma, attenzione, sebbene si tratti di elementi prefabbricati, sono realizzati a partire da matrici fatte ad hoc: le soluzioni standard non sono contemplate in Gualini, grazie anche al know how acquisito negli anni con committenze molto prestigiose. Infatti, lo ritengono un approccio molto limitativo dal punto di vista progettuale, così i prodotti si caratterizzano per la loro unicità industrializzata, quasi un ossimoro, ma in pratica a una fase di ideazione segue necessariamente quella di progettazione personalizzata.
Una singolarità che implica una fase di collaudo lunga e onerosa perché non basta garantire l’estetica, ma anche la performance dell’involucro dell’edificio, prima di passare alla produzione, al trasposto e infine alla posa, la parte sicuramente con meno rischi e più impersonale secondo l’azienda bergamasca.
E non a caso nello stabilimento Gualini c’è uno dei più grandi banco prova presenti in Italia, dove simulare diverse condizioni meteo come acqua aria e vento. Successivamente si produce in linea di circa 100-120 metri, si assembrano i primi componenti e passo dopo passi la cellula arriva fino al controllo qualità per essere imballata e spedita.
Nel caso del grattacielo 262 si tratta di cellule dalle dimensioni fuori dagli standard perché misurano 4 metri per 3,50 metri, ma trasportate nella posizione d’installazione in cantiere dove sono stati preventivamente posati i sistemi di fissaggio. Ecco, se anche questa fase finale se non è stata progettata a monte, l’istallazione diventa molto più onerosa e incerta.
di Monica Battistoni